Go wireless and take predictive maintenance to the next level!
Many manufacturers are today looking at the possibilities of implementing predictive maintenance and embracing digitalisation. With this post we want to explain the importance of choosing a wireless connectivity that can take your predictive maintenance solutions to the next level!
Already in the 1950s the concept “condition-based monitoring”, CBM, was introduced in the industry to predict impending failures early enough to save components and over time the concept predictive maintenance has evolved. However, the final target is still to determine the condition of a machine and detect problems before they cause downtime. To me, the big difference between condition based monitoring and predictive maintenance is the amount of gathered data and how the data is used. Simply – The more historical condition based data that is available, the better and more accurate predictive maintenance can be done.
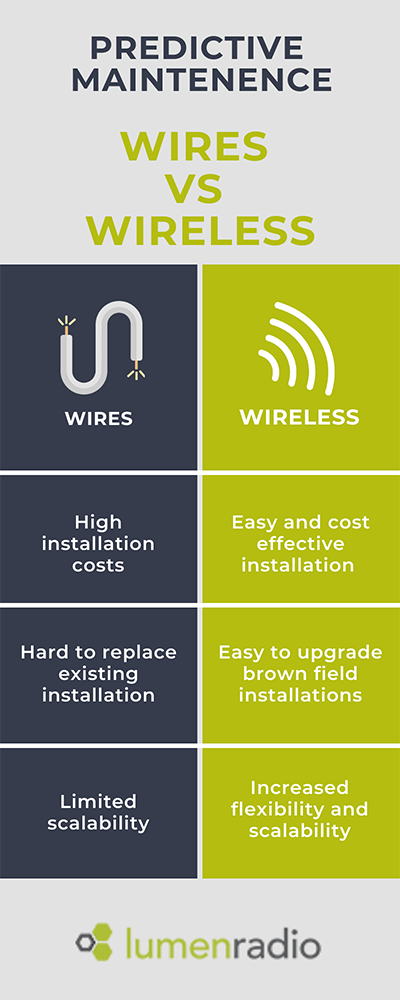
High installation costs
It’s easy to see the beauty in predictive maintenance and one may wonder why the method is not used everywhere when the advantages over planned maintenance are so significant. The simple answer is because of high installation costs. When the decreased maintenance cost is less than the increased installation cost the willingness to invest in new systems is very low.
Until now, wired sensor has been the only reliable alternative but it entails disadvantages such as purchasing of expensive cables, hours of installation work and limitation in scalability. Not to mention all the instruments equipped with diagnostics about the process that is unused because of the difficulties it implies to install wired connections in the field. I could go on but I guess you got the point.
The right wireless technology
Now imagine if countless different sensors could be mounted wirelessly anywhere in a harsh industrial environment. All connected to each other in a perfectly applied meshed network, running on battery or energy harvesting technology. Then picture yourself that the wireless connection is even more reliable and robust in comparison to wired solutions.
With LumenRadio’s Cognitive Coexistence technology in combination with a meshed network and firmware-over the air updates (FOTA) this scenario is not fictive anymore but rather the reality of today.
With Future-Proof radio technology predictive maintenance will be applied more widely than ever. For the end customer, this means easier installation, lower installation cost, increased flexibility and scalability but also improved profitability as the service life of the machine will be optimally managed.
It is the ability to collect and process large amount of information that will boost your manufacturing. With the right technology for wireless vibration monitoring more sensors can be connected gathering more data for your decisions. More connected sensors implies a higher demand for interference management. This is why choosing the right wireless connectivity technology will be crucial for the future success of your business, so don’t settle for mediocre standards.